Meeting customers’ demands through automation can be revolutionary in the fast-paced packaging industry, particularly when it comes to assuring production efficiency and optimizing processes. Tray denesters are an indispensable piece of equipment for businesses that use trays to store and transport goods. However, how can you pick the best tray denester to suit your particular requirements when there are so many possibilities available? We’ll go over the key points in this guide to assist you in making an informed choice.
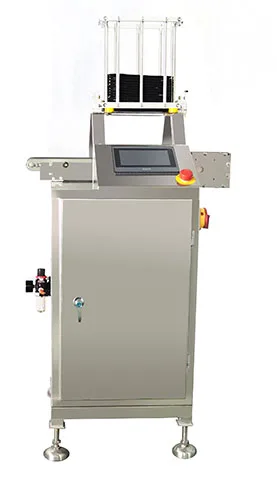
What are the main factors when choosing the right tray denesting machines?
1. Assess Your Production Volume
The first question to ask is about your production volume. High-speed denesters can handle hundreds of trays per minute, making them ideal for large-scale operations that require fast, consistent performance. Smaller operations, however, may find that a lower-speed denester is more than adequate—and more cost-effective. Aligning your denester choice with your production volume ensures you invest only in the capacity you need.
2. Consider Tray Types and Materials
Tray denesters come in different configurations, with each unit designed to handle various types of trays. If your business uses trays made from plastic, foil, or biodegradable materials, or if you require special tray shapes, choose a denester that’s compatible with those specifics. Some denesters are highly specialized, while others are designed for flexibility, handling multiple tray types and sizes on the same line. Ensuring compatibility with your trays will minimize downtime and prevent costly errors on the production line.
3. Know Your Tray Gap When Stacked
Tray spacing, or the gap between trays when stacked, is a critical factor that can impact the performance of your tray denester. If your trays are tightly stacked with minimal gaps, some denesters may struggle to separate and dispense them efficiently, leading to potential jams or slowdowns. Conversely, trays with larger gaps are an easier job for a denester to ensure smooth feeding.
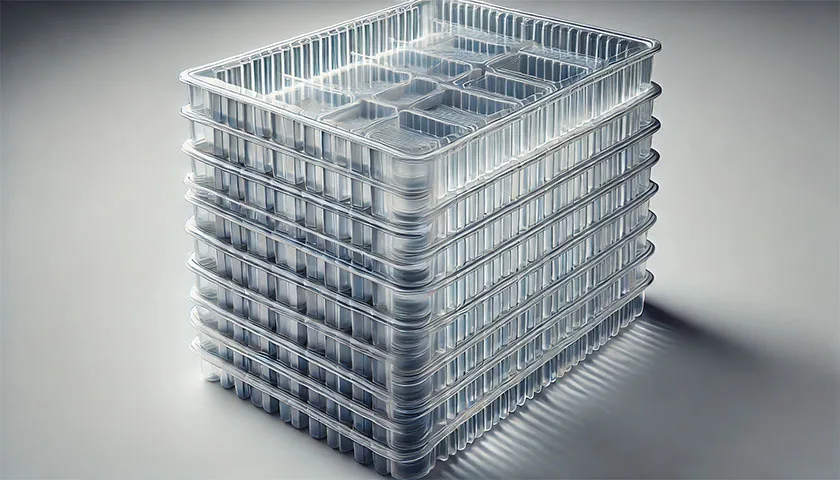
Evaluating your tray stack gap and choosing a denester designed to accurately place the trays will help maintain a steady flow on your production line, reducing downtime and maximizing throughput.
There are several types of tray denesters available, each designed to meet different needs and applications. Some common types of tray denesters include:
- Screw Type Tray Denesters: These denesters use a screw mechanism to separate trays from a stack and are suitable for containers with a consistent gap when stacked.
- Insert Type Tray Denesters: these denesters using valve to control the seperate action, the device will insert the gap of trays then move down to separate. They are suitable for big tray gap when stacked.
- Pick and Place Type Tray Denseter: they use grippers to precisely picke trays from stack then place it on the production line, ideal for facilities handling diverse tray types or needing exact positioning.
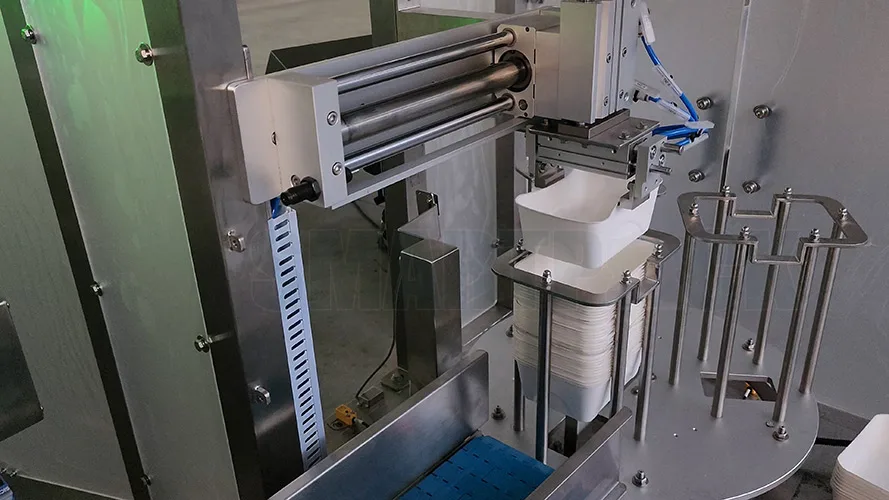
4. Evaluate Space Constraints
Space is often at a premium in production facilities, so it’s important to consider the physical footprint of your equipment. Tray denesters come in both compact models, ideal for small or limited spaces, and larger, more robust units for high-capacity needs. Measure your space carefully and think about how the denester will fit within your existing layout, alongside other machines in your packaging line.
5. Look for User-Friendly Features
Today’s tray denesters often come with advanced features designed to simplify operation and maintenance. Look for models with intuitive touchscreen controls, quick-change functionality, and easy-to-access parts that allow for minimal interruptions when switching tray sizes or conducting routine maintenance. These features don’t just make operation easier—they also improve productivity and reduce the risk of human error.
One valuable feature offered by Smartpack, is an extra empty trays feeding device. This add-on automates the process of loading empty trays into the denester, reducing manual labor and keeping your line moving efficiently. These features not only make operation easier—they also improve productivity and reduce the risk of human error.
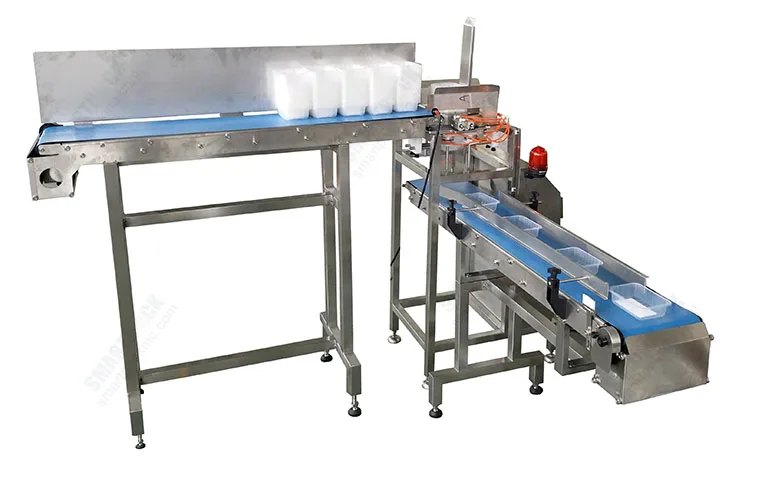
6. Handling Multiple Tray Stacks
Handling multiple tray stacks is a common challenge in the packaging industry. To address this challenge, tray denesters can be designed to handle multiple stacks simultaneously. Smartpack designes and produced 2 or even 3 trays denester. By handling multiple tray stacks, food manufacturers can increase productivity, reduce labor costs, and improve overall efficiency.
7. Factor in Integration Needs
If your tray denester will be part of a larger automated system, compatibility is key. Machines like the place denester can seamlessly integrate with other packaging equipment—like form-fill-seal machines, case packers, or labeling machines—providing a smoother workflow and helping reduce bottlenecks. Be sure to discuss integration options with your equipment supplier, especially if you plan on future expansions or updates to your production line.
Smartpack has well experienced at the intergrated packaging system, you can get more effective solutions and more efficient communication here.
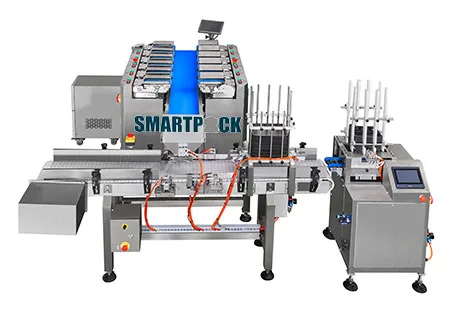
8. Prioritize Reliability and Support
Even the best equipment needs regular upkeep, and choosing a denester backed by strong support can save your team time and frustration. Look for a manufacturer or supplier known for providing quick-response technical support, readily available replacement parts, and comprehensive service plans. A reliable support team helps you maintain maximum uptime and achieve the full potential of your tray denester investment.
9. Quality and Performance
When it comes to tray denesters, quality and performance are critical factors to consider. A high-quality tray denester should be able to accurately and efficiently denest trays, while also minimizing downtime and maintenance. Look for denesters that are built with durable materials, have a simple and intuitive design, and are easy to integrate with existing production lines. Additionally, consider denesters that offer advanced features, such as high-speed denesting, gentle handling of delicate trays, and customizable solutions to meet specific needs. By investing in a high-quality tray denester, manufacturers can improve productivity, reduce costs, and enhance overall performance.
10. Customize for Specific Requirements
In some cases, off-the-shelf solutions may not meet the exact needs of your operation. Custom denesting solutions, tailored to specific tray shapes, product handling requirements, or unique production speeds, can be the answer. Companies like Viking Masek are known for creating custom packaging solutions, ensuring that your tray denester is optimized to deliver the performance and efficiency you need for your specific products and workflows.
Final Thoughts
Tray denesters are an essential component in the packaging process, designed to efficiently and accurately denest trays from a stack. These machines play a critical role in ensuring that trays are ready for product loading on the production line. By automating the denesting process, tray denesters can significantly improve productivity, reduce labor costs, and minimize the risk of errors. With a wide array of tray denesters available, manufacturers can choose the best solution for their specific needs, from high-speed denesting to gentle handling of delicate trays.
Selecting the right tray denester can have a lasting impact on your production efficiency and product quality. By assessing your production needs, evaluating machine compatibility, and choosing a reliable supplier, you can ensure that your investment drives productivity and meets your business goals for years to come.