Introduction: Why You Should Care About Automation in Laundry Pod Packaging
If you’re involved in laundry pod production, or even just curious about how the packaging process works, then you’re in the right place. Let’s dive into why automation in laundry pod packaging is not just a passing trend but an essential move for any manufacturer looking to improve their bottom line and meet the demands of a fast-paced market.
From speed and efficiency to precision and cost-effectiveness, automation is a revolutionary. In fact, it’s hard to imagine a laundry pod packaging operation functioning without automated systems in today’s competitive environment.
So, if you’re still relying on manual labor for packaging, you’re probably wasting time and money, and risking your product’s consistency. This article will break down exactly why automating your laundry pod packing line is crucial for long-term success.
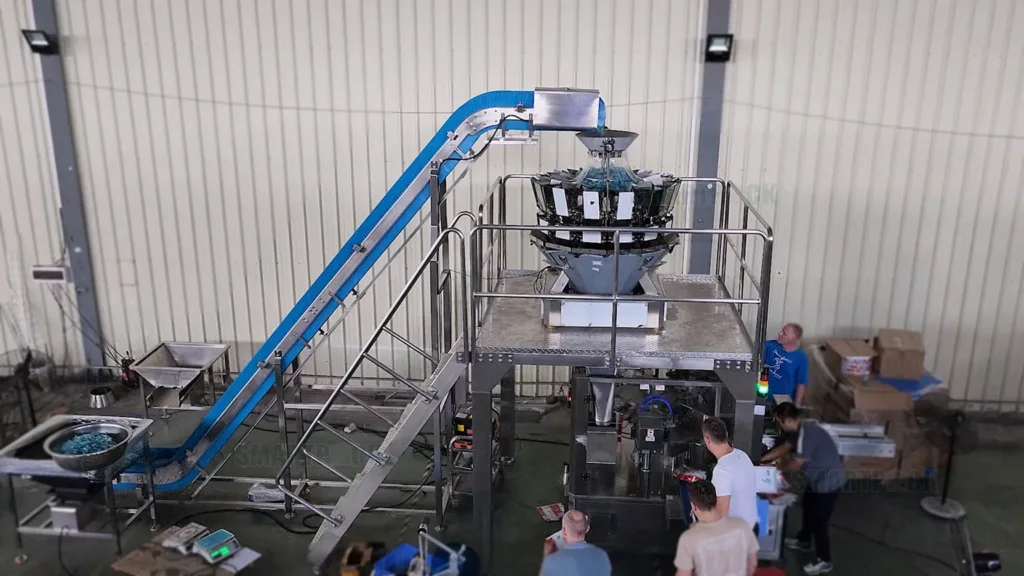
Speed and Efficiency: Getting More Done in Less Time
Streamlining the Packaging Process
Imagine packing hundreds or thousands of laundry pods by hand. It’s time-consuming, inconsistent, and, frankly, inefficient. Not to mention, it requires a lot of human labor, which means more potential for errors. Automated systems, on the other hand, can handle high-volume tasks with incredible speed.
With automation, the process of filling, counting, sealing, and labeling pods can be completed in a fraction of the time it would take with a manual process. The result? You can produce and package far more laundry pods in the same amount of time, improving overall productivity and ensuring that you meet market demands.
Meeting Demands for Faster Production
In today’s world, speed is everything. Customers want their laundry pods as quickly as possible, and retailers want to keep their shelves stocked with minimal lag time. With automation, production can be ramped up easily to meet increasing consumer demand without worrying about manual labor limitations.
Automation allows you to keep up with tight production schedules while maintaining a consistent level of quality. Instead of relying on a handful of workers to complete the tasks, machines take over, speeding up each step of the process without losing any of the necessary quality checks.
Automated systems can increase your production speeds by up to 50%, meaning you’ll get more done in less time. This is essential for staying competitive in today’s fast-moving marketplace.
Accuracy and Consistency: Getting It Right Every Time
Precision in Packaging
When it comes to laundry pod packaging, precision is paramount. Pods are small, and each package needs to be filled correctly. If the pods are underfilled or overfilled, not only could you be short-changing customers, but you could also run into issues with product consistency. Customers expect their pods to be uniform in size and weight, and manual processes simply can’t deliver that level of accuracy with the same speed.
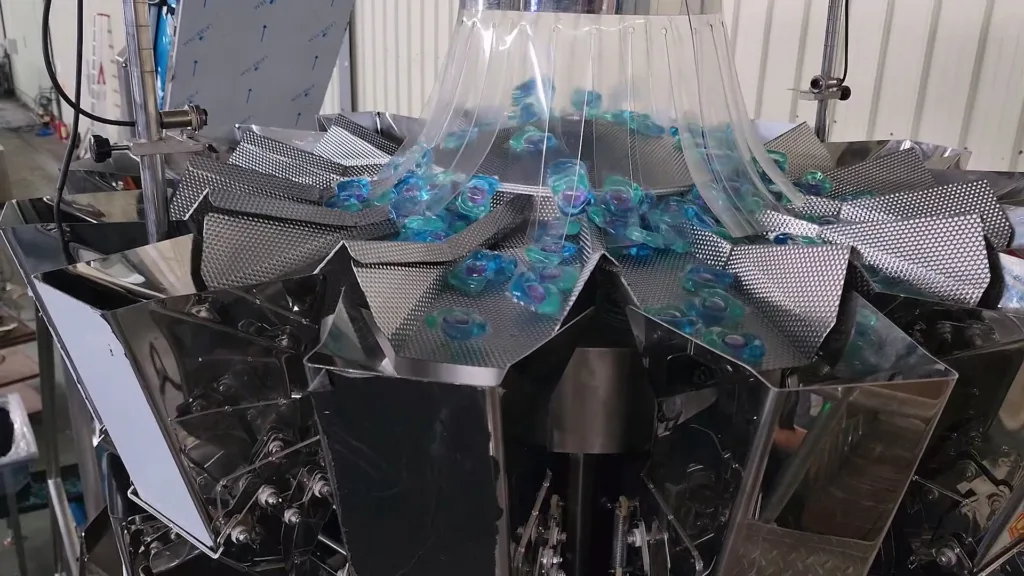
Automated machines ensure that every pod is counted and filled accurately, with no risk of human error. In fact, many machines come equipped with built-in sensors and quality-control checks, which further minimize the chance of mistakes.
Maintaining Quality Across the Board
When you rely on manual labor, there’s a good chance that no two packages will look the same. Inconsistencies, even small ones, can affect your brand’s reputation and lead to dissatisfied customers. Automated packing systems standardize the process, ensuring that each laundry pod package is identical in weight, size, and labeling.
This level of consistency is particularly important when you’re dealing with a mass-market product like laundry pods, where consumers expect the same product quality every time they make a purchase.
Automation ensures 100% accuracy in filling and packaging, leading to consistent products that reinforce customer trust in your brand. This consistency isn’t just nice to have—it’s essential for maintaining a loyal customer base.
Cost Efficiency: Saving Money in the Long Run
Cutting Down on Labor Costs
Manual labor is expensive. Between wages, training, and employee benefits, the cost of staffing a manual packaging line adds up quickly. But with automated systems, you can significantly reduce the number of workers needed to run your packaging line. This frees up resources for other parts of the business, like innovation or marketing, and ultimately helps cut overall operational costs.
Automated machines can also reduce the chances of costly errors or downtime due to human fatigue. Unlike manual workers, automated machines don’t need breaks, and they can work around the clock without sacrificing performance.
Less Waste, More Savings
In manual packing lines, waste is inevitable. From spillage during filling to over-packaging, there are many points where material and product can be lost. With automated packing systems, the chance of this happening is minimized. The machines ensure precise fills, eliminate over-packaging, and ensure that you’re getting the most out of your raw materials.
Additionally, automation allows for better material management, optimizing the use of packaging materials such as plastic wraps, bags, and labels. This reduces the overall waste produced, which translates to cost savings in materials.
Automation can reduce labor costs by up to 40% and material waste by 30%, resulting in a more cost-efficient operation in the long term.
Flexibility: Adapting to Market Changes
Quickly Adjusting to New Demands
One of the most overlooked benefits of automation is its flexibility. If the market changes or if there’s a demand for a different size or type of packaging, automated machines can easily be reprogrammed or adjusted. For example, a new type of laundry pod or packaging format can be integrated into your existing system with little hassle.
Manual systems, on the other hand, require workers to physically make changes, which takes more time and costs more money. Automated systems give you the flexibility to experiment with new products or packaging options without having to overhaul your entire operation.
Future-Proofing Your Operations
As consumer demands evolve, so does the market. By investing in automated systems now, you’re essentially future-proofing your production line. Whether it’s a change in packaging design, product size, or materials, automated systems can be adapted quickly and easily, meaning you won’t have to reinvest in new equipment every time there’s a shift in demand.
This flexibility ensures that your production line remains agile and capable of handling whatever comes next—whether it’s new customer expectations, new regulations, or new competition.
Automation gives your business the flexibility to adapt quickly to new trends, packaging formats, or production needs, ensuring your operations stay ahead of the curve.
Conclusion: Embrace Automation for a Better Future in Laundry Pod Packaging
The future of laundry pod packaging is clear: it’s automated. With its ability to increase speed, ensure accuracy, reduce costs, and provide flexibility, automation is not just an option; it’s a necessity.
By embracing automation, you can streamline your production process, maintain consistency, and reduce operational costs—all while staying ahead of the competition. Whether you’re a small manufacturer or a large-scale operation, automation is the key to long-term success in the laundry pod packaging industry.