The purpose of this guide is to provide a comprehensive overview of all the factors to consider when buying a jar packing machine. It aims to assist you in making an informed decision by helping you choose a machine that meets your production needs and budget. Furthermore, it highlights industry-specific considerations, addressing unique requirements based on your particular industry.
Who Needs Jar Packing Machines?
Jar packing machines are essential for various industries that require efficient and hygienic packaging solutions:
- Food and Beverage Manufacturers: For packaging jams, sauces, spices, and beverages.
- Pharmaceutical Companies: For bottling medicines, supplements, and health products.
- Cosmetic Producers: For creams, lotions, and beauty products.
- Chemical Industries: For packaging chemicals, adhesives, and other industrial products.
Understanding Jar Packing Machines
What Is a Jar Filling and Packing Machine?
A jar packing machine is specialized equipment designed to automate the process of filling, sealing, capping, and labeling jars. These machines can handle various jar sizes and materials, integrating seamlessly into production lines to enhance efficiency.
- Basic Functionalities:
- Filling: Dispensing the exact amount of product into each jar.
- Capping: Sealing jars securely to preserve product integrity.
- Labeling: Applying labels accurately for branding and compliance.
- Extra Functionalities:Empty jars washing and dryingEmpty jars UV Sterilization
- Role in Automated Production Lines: They reduce manual labor, minimize errors, and ensure a smooth and continuous packaging process.
Benefits of Using Jar Packing Machines
- Increased Speed and Efficiency: Machines can operate continuously at high speeds, significantly boosting production rates.
- Consistency and Precision: Automated systems ensure each jar is filled and sealed to the same specifications, enhancing product quality.
- Reduction in Labor Costs: By automating repetitive tasks, you can allocate human resources more effectively and reduce staffing needs.
- Adaptability to Market Demand: Jar packing machines can adapt to market demand for various products, enhancing their efficiency and consistency.
Types of Jar Packing Machines
Understanding the different types of jar packing machines will help you select the one that best suits your needs.
Based on Automation Level: Automatic Filler
Manual Machines
- Ideal for small-scale operations with lower production volumes.
- Require significant human intervention.
Semi-automtic Machines
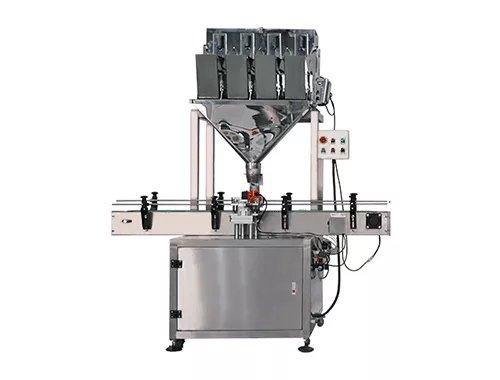
- A blend of manual and automated functions.
- Suitable for medium-sized businesses looking to increase efficiency without a significant investment.
Fully Automatic Machines
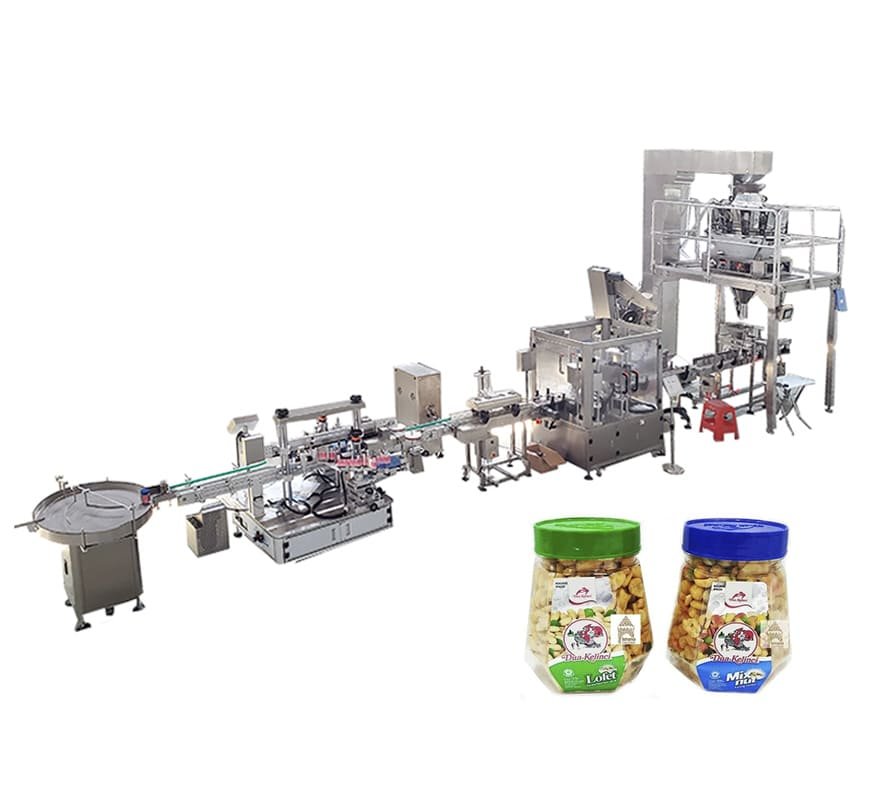
- Best for high-speed, large-scale production.
- Minimal human intervention required, leading to consistent output and quality.
Based on Functionality
- Filling Machines:
- Designed to dispense precise amounts of product into jars.
- Can handle various product viscosities, from granule, liquids to pastes.
- Capping Machines:
- Automate the process of sealing jars with caps or lids.
- Ensure tight seals to preserve product freshness.
- Labeling Machines:
- Apply labels accurately and efficiently.
- Can handle different label sizes and types.
- Integrated Systems:
- Combine filling, capping, and labeling functions into one machine.
- Offer seamless operation and save space.
Key Features to Consider
When evaluating jar packing machines, consider the following features to ensure the machine meets your specific needs.
Speed, Efficiency, and Production Capacity
Production Capacity:
- Measured in jars per minute or hour.
- Choose a machine that can handle your current and projected future volumes.
- The filling volume can be adjusted to meet specific production needs, enhancing the machine’s efficiency.
Changeover Times:
- The time required to switch between different jar sizes or products.
- Machines with quick changeover capabilities reduce downtime.
Compatibility with Jar Specifications
- Sizes and Shapes:
- Ensure the machine jar can accommodate the range of jar sizes and shapes you use.
- Materials:
- Machines should handle the types of jars you use, whether glass or plastic.
Material and Build Quality
- Durability:
- Look for machines made with high-quality components to ensure longevity.
- Construction Materials:
- Stainless steel is preferred, especially in food and pharmaceutical industries, for its hygienic properties and resistance to corrosion. Aluminum foil is also crucial in the sealing process, as it creates a hermetic seal when heated by electromagnetic induction, enhancing product longevity and preventing leakage.
Automation and Control Systems
- User Interface:
- An intuitive interface makes the machine easier to operate and reduces training time.
- Programmable Settings:
- Ability to save settings for different products improves efficiency during changeovers.
Safety Features
- Emergency Stop Buttons:
- Essential for operator safety to halt the machine immediately in case of issues.
- Guarding and Safety Interlocks:
- Prevent access to moving parts while the machine is operating.
- A sealing machine is crucial in ensuring high performance and safety in the packaging process, as it helps maintain the integrity and hygiene of the packaged products.
Maintenance and Support
- Ease of Cleaning:
- Machines designed for easy cleaning reduce downtime and improve hygiene.
- Maintenance Routines:
- Regular maintenance extends the machine’s lifespan; consider how easy it is to perform routine checks.
- Availability of Spare Parts and Technical Support:
- Ensure the supplier provides readily available parts and responsive support.
Technical Specifications
Understanding technical specifications helps you assess whether a machine fits your operational needs.
Filling Range and Accuracy
- Volume Capacities:Machines should handle the volume range required for your products, including efficient jar filling for various types of products, from liquids to pastes, with options for automatic and semi-automatic jar filling machines.
- Tolerances and Precision Levels:High precision reduces product waste and ensures consistency.
Power and Energy Requirements
- Electrical Specifications:Check voltage and phase requirements to match your facility’s power supply.
- Energy Efficiency Ratings:Energy-efficient machines lower operating costs and are better for the environment.
Dimensions and Space Requirements
- Machine Footprint:Ensure the machine fits within your available floor space, not only focusing on length and width, machine height should be paid attention.
- Accessibility:Adequate space around the machine is necessary for operation and maintenance.
Noise Levels
- Compliance with Regulations:Machines should meet workplace noise regulations to ensure a safe environment.
- Operator Comfort:Lower noise levels improve working conditions for staff.
Cost Considerations
Understanding the total cost of ownership helps in budgeting and evaluating the machine’s value over time.
Initial Investment
- Purchase Price:Obtain detailed quotes, including all necessary components and accessories.
- Financing Options:Explore leasing or financing if upfront costs are a concern.
Operating Costs
Energy Consumption:
More efficient machines reduce long-term energy costs. An efficient packaging line can further reduce these costs by optimizing the entire process, from filling to capping and labeling.
Labor Requirements:
Automated machines may reduce staffing needs, lowering labor costs.
Maintenance Costs
- Scheduled Servicing:
- Regular maintenance costs should be factored in.
- Potential Downtime Costs:
- Reliable machines minimize production interruptions.
Return on Investment (ROI)
- Calculating Payback Period:
- Estimate how long it will take for the machine to pay for itself through increased efficiency and reduced costs.
- Long-Term Financial Benefits:
- Consider how the machine will impact profitability over its lifespan.
Supplier Evaluation
Choosing the right supplier is as important as selecting the right machine.
Reputation and Experience
Industry Standing: Suppliers with a solid track record are more likely to provide reliable equipment. Their expertise in providing reliable packaging machines, designed for filling, sealing, and labeling various product forms, ensures efficient and customized solutions.
Specialization Areas: Suppliers experienced in your industry understand specific needs.
Customer Support and Service
- Training Programs:
- On-site training ensures your staff can operate the machine effectively.
- Technical Assistance Availability:
- Responsive support minimizes downtime during issues.
Warranty and After-Sales Service
- Coverage Details:
- Understand what parts and services are covered and for how long.
- Service Agreements:
- Consider extended warranties or service contracts for additional peace of mind.
Customer Reviews and Testimonials
- Case Studies:
- Real-world examples demonstrate how the supplier has met other clients’ needs.
- References:
- Speaking with existing clients can provide insights into the supplier’s reliability.
Regulatory Compliance
Ensuring your machine meets all relevant regulations is crucial to avoid legal issues and maintain product quality.
International Standards
- CE Marking:
- Indicates compliance with European safety, health, and environmental protection standards.
- ISO Certifications:
- Certifications like ISO 9001 demonstrate quality management systems.
Food Industry Regulations
- Sector-Specific Requirements:
- Verify that the machine complies with regulations specific to your industry and region.
Environmental Regulations
- Waste Management:
- Machines should minimize waste and support recycling efforts.
- Energy Consumption Standards:
- Compliance with energy efficiency regulations reduces environmental impact.
Future-Proofing Your Investment
Consider how the machine will fit into your long-term plans.
Scalability
Capacity for Expansion:
Machines that can be upgraded or expanded accommodate business growth. The use of a star wheel in these machines ensures they can handle jars of various sizes, facilitating smooth operation during the filling and capping process.
Modular Design:
Allows adding new features or capabilities as needed.
Customization Options
Tailoring to Specific Needs:
Customizable machines can better meet unique production requirements. These machines are versatile enough to handle different products, including edible oil and salad dressings, ensuring proper sealing and filling to maintain product quality and extend shelf life.
Flexibility:
Machines that handle a variety of products and packaging types offer greater versatility.
Conclusion
Recap of Key Points
Selecting the right jar packing machine involves careful consideration of various factors, including:
- Production Needs: Aligning machine capabilities with your production volume and product types.
- Quality and Compliance: Ensuring the machine meets industry standards and regulatory requirements.
- Cost and ROI: Evaluating both initial and ongoing costs against the expected benefits.
Final Tips
- Prioritize Essential Features: Focus on features that directly impact your production efficiency and product quality.
- Consider Total Cost of Ownership: Look beyond the purchase price to include operating and maintenance costs.
- Seek Expert Advice: Consult with suppliers and industry experts to gain insights.
Next Steps
- Request a Quote: Reach out to reputable suppliers with your specific requirements.
- Arrange Demonstrations: Seeing the machine in action can help assess its suitability.
- Consult Your Team: Involve operators and maintenance staff in the decision-making process.
FAQs
- How do I determine the right size of the jar packing machine for my operation?
- Assess Production Volume: Calculate your current and projected production needs.
- Consider Space Constraints: Ensure the machine fits within your facility.
- Consult with Suppliers: They can recommend models based on your requirements.
- What kind of maintenance does a jar packing machine require?
- Regular Cleaning: Prevents contamination and maintains hygiene.
- Lubrication: Keeps mechanical parts functioning smoothly.
- Inspection of Components: Early detection of wear and tear prevents breakdowns.
- Can jar packing machines handle different types of products?
- Adjustable Settings: Many machines can be adjusted for various products.
- Check Compatibility: Verify with the supplier if the machine can handle your specific products.
- How long does it take to install and set up the machine?
- Installation Time Varies: Depends on the machine’s complexity and your facility.
- Supplier Coordination: Work with the supplier to establish a realistic timeline.
- Is training provided with the purchase of the machine?
- Most Suppliers Offer Training: Ensures your staff can operate and maintain the machine effectively.
- Ask About Training Programs: Confirm what training is included and if additional training is available.