Introduction
Snack manufacturers face mounting pressure to increase production speed while maintaining product quality and minimizing costs. As consumer demands rise, the need for consistent, efficient, and scalable packaging solutions becomes more critical. This is where fully integrated automation in snack packaging comes into play. By automating the entire packaging process, manufacturers can achieve higher production speeds, improve consistency, reduce operational costs, and remain competitive in a fast-paced market.
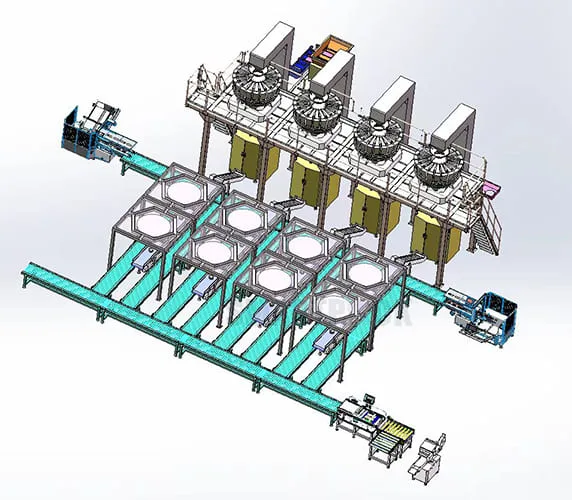
In this guide, we will explore how integrating key machines in the snack packaging process creates a seamless, high-efficiency production line. From the raw material handling to final palletizing, each machine plays a vital role in optimizing the flow of operations, ensuring that snack products are packed and shipped faster than ever before.
The Benefits of Fully Integrated Snack Packaging Systems
Implementing a fully integrated snack packaging system brings multiple benefits to manufacturers, all of which contribute to improved efficiency, reduced costs, and higher-quality products.
Increased Efficiency
The automation of each stage in the snack packaging process minimizes delays and bottlenecks. With the right systems in place, manufacturers can achieve continuous operations, reducing downtime and speeding up the overall production cycle. This results in faster output and allows manufacturers to meet high production demands without compromising quality.
Cost Reduction
Labor costs are often one of the largest expenses in the manufacturing process. By automating tasks like weighing, filling, sealing, and palletizing, snack manufacturers can reduce the need for manual intervention, cutting down on labor expenses. Additionally, automation reduces errors, prevents waste, and minimizes product rework, which further contributes to cost savings.
Consistency & Quality Control
Automated systems provide precise control over the production process. With machines handling repetitive tasks like weighing, filling, and sealing, the risk of human error is eliminated, ensuring uniformity in product weight, portion size, and packaging quality. This not only improves the consistency of the final product but also enhances the overall customer experience.
Scalability
Automated systems are designed to scale. As production demands increase, manufacturers can easily add more machines or upgrade existing systems without the need to hire additional labor. This scalability ensures that snack manufacturers can keep up with market trends and consumer needs without facing significant operational challenges.
Key Machines in an Integrated Snack Packaging Line
A fully integrated snack packaging line consists of several specialized machines, each playing a unique role in the overall process. Let’s take a closer look at the machines that make this integration possible.
1. Bucket Conveyor
Function: The bucket conveyor efficiently transports snacks (such as chips, nuts, or crackers) from one station to the next in the production line. It uses buckets or containers mounted on a continuous loop to move the product.
Advantages: The bucket conveyor helps maintain consistent flow throughout the packaging line, reducing product spillage and damage. Its enclosed design also minimizes contamination risks and protects the snacks from dust or other environmental factors.
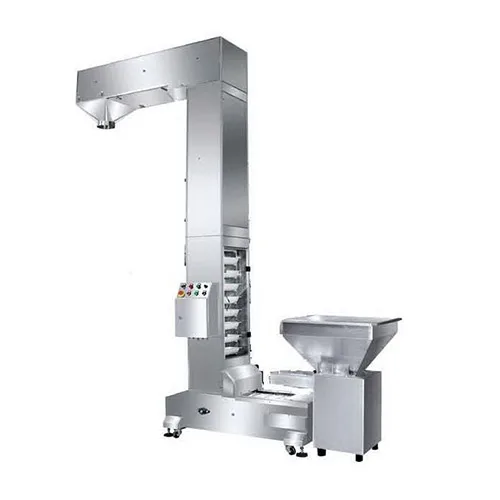
2. High-Speed Multihead Weighers
Function: Multihead weighers are used to weigh snacks in various sizes or portion configurations. These systems use multiple weighing heads to collect, process, and combine small batches of snack products to achieve precise total weights.
Advantages: High-speed multihead weighers can perform weighing operations at very fast rates with extreme accuracy. They help ensure that every package contains the correct amount of product, reducing waste and ensuring compliance with packaging standards.
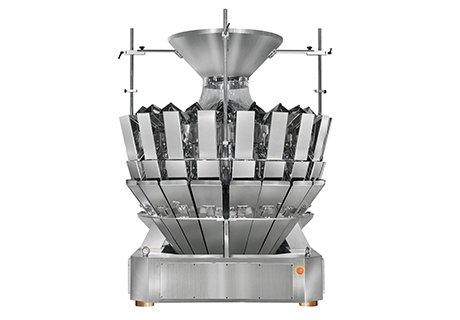
3. Continuous Motion Vertical Form-Fill-Seal Packaging Machines
Function: These machines are used to form, fill, and seal snack bags automatically. The vertical form-fill-seal (VFFS) machines take a roll of film, form it into a tube, fill it with the product, and then seal the bag in one continuous motion.
Advantages: Continuous motion VFFS machines are ideal for high-speed operations, as they allow for continuous bag production without interruption. They also provide high-quality seals and consistent package sizes, which is essential for ensuring product safety and consumer satisfaction.
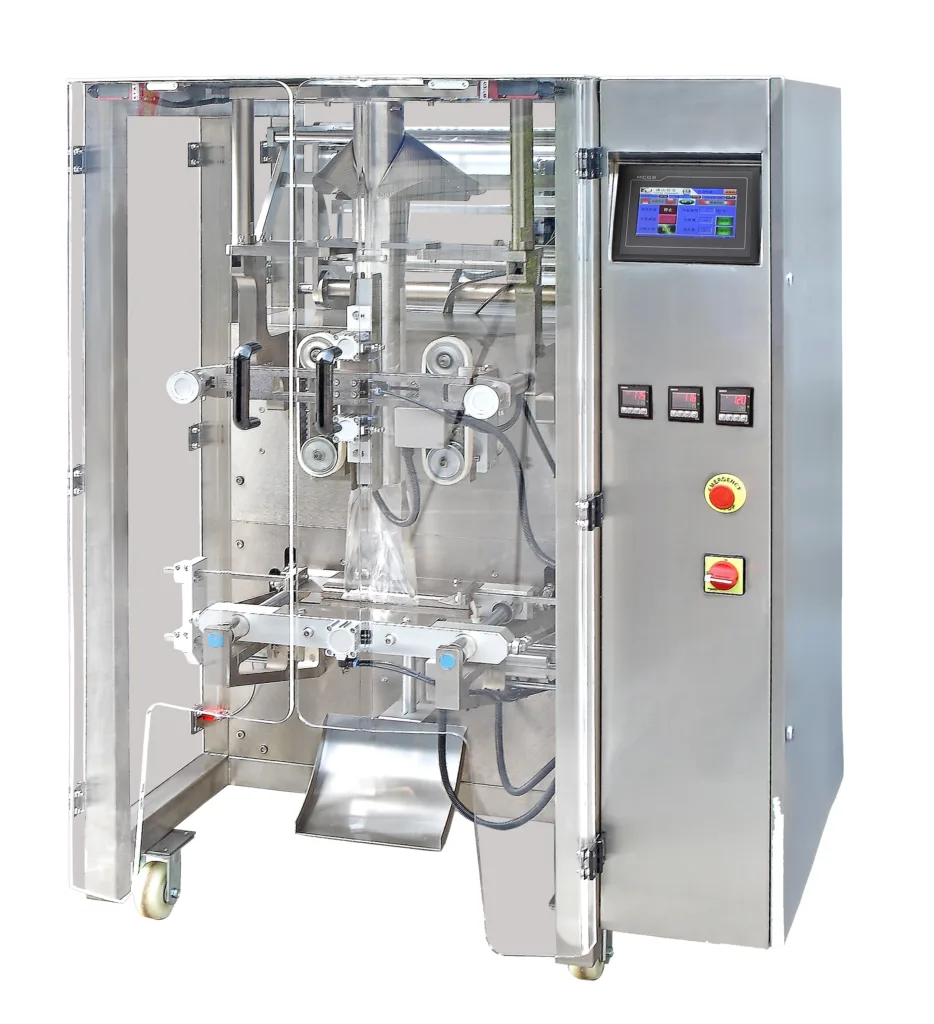
4. Support Platforms
Function: Support platforms provide structural support for integrating various machines in the production line. These platforms elevate and stabilize machinery, allowing for a streamlined, organized flow of operations.
Advantages: A well-designed support platform maximizes space efficiency and allows easy access for operators and maintenance staff. It also ensures that machines are aligned properly, which is crucial for maintaining synchronization in an automated system.
5. Output Conveyor
Function: The output conveyor moves the packaged snacks, now in their sealed cartons, to the next step in the process or directly to storage and shipping areas.
Advantages: The output conveyor facilitates smooth and continuous transportation of finished products. It optimizes space, prevents bottlenecks, and maintains a steady flow of products ready for shipment.
Enhancing the Packaging Flow
Once the snacks are weighed, filled, and sealed, they move through the next stages of the packaging line. This section will focus on the machines that handle the next steps: ensuring the accuracy of the final product and preparing it for storage and shipping.
1. Checkweigher
Function: A checkweigher is used to verify that the weight of each packaged snack meets the required specifications. The checkweigher automatically weighs each package as it moves along the line, checking its weight against predefined limits. It also can be used for weighing the carton weight in the next packaging process.
Advantages: Checkweighers ensure that every package is accurately filled, preventing underfilled or overfilled packages. This reduces waste, ensures compliance with industry regulations, and maintains brand reputation for providing consistent products.
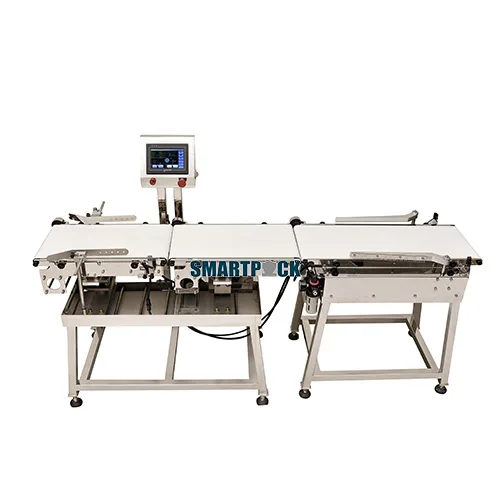
2. Case Erector
Function: The case erector automatically forms flat cardboard boxes into their correct shape, ready for filling. This machine is essential for packaging large quantities of snack bags into boxes.
Advantages: The case erector saves time and labor by automating the box formation process. It ensures that boxes are consistently shaped and sturdy, ready to withstand transport and handling without damage.
3. Case Sealer
Function: After snack bags are packed into cartons, the case sealer securely seals the boxes with tape or glue, preventing the contents from spilling out during transport.
Advantages: Case sealers improve the security of the package, ensuring that each carton is sealed tightly and properly. This reduces the risk of packaging failure and ensures the products are safely stored and shipped.
Automation for Final Packaging and Palletizing
1. Palletizing Robot for Cartoning (Snack Bags into Cartons)
Function: The palletizing robot is responsible for picking individual snack bags and placing them into cartons. This machine automates the critical step of preparing snacks for final shipping and storage.
Advantages: The use of a palletizing robot increases speed and precision in placing snack bags into cartons, eliminating the need for manual labor. It improves operational efficiency, reduces the risk of human error, and ensures that products are safely packed for transport.
2. Portable Palletizing Workstation (Cartons onto Pallets)
Function: The portable palletizing workstation automatically picks up sealed cartons and places them onto pallets in a pre-determined pattern. The workstation is mobile, allowing flexibility in different parts of the production facility.
Advantages: The portability of the palletizing workstation allows manufacturers to optimize the layout of their production line based on changing needs. It reduces manual labor and improves the safety and efficiency of the final palletizing process by ensuring cartons are stacked securely and uniformly.
How These Machines Work Together in an Integrated System
The success of a fully automated snack packaging line relies on the seamless integration of all the machines discussed above. From the initial conveyor system to the final palletizing workstation, each machine works together to create a continuous, synchronized process.
By connecting machines like bucket conveyors, multihead weighers, VFFS packaging machines, checkweighers, and palletizers, manufacturers can achieve higher throughput, reduced downtime, and better-quality products. Integration also allows for real-time monitoring of the entire line, enabling manufacturers to identify and address issues quickly.
Key Considerations for Implementing an Automated Packaging Line
When implementing a fully automated snack packaging line, manufacturers need to consider several factors to ensure success.
Choosing the Right Equipment
It’s important to choose machines that are best suited to your specific production requirements, whether that’s based on the snack type, packaging format, or production volume.
Customization Options
Automation lines can often be customized to accommodate different snack products or packaging styles, ensuring flexibility as product lines evolve.
Space and Layout Planning
Optimizing space for each machine is crucial to avoid congestion in the production area and maximize operational flow. Proper layout planning ensures that the production line remains efficient and safe.
Training & Maintenance
Regular staff training and machine maintenance are essential for keeping the production line running smoothly. Training ensures that operators understand how to use the equipment, and maintenance prevents breakdowns that could disrupt operations.
The Future of Snack Packaging Automation
As technology continues to advance, snack packaging systems will become even more automated and efficient. Manufacturers are increasingly turning to energy-efficient machines, eco-friendly materials, and automated solutions that reduce their carbon footprint.
Conclusion
Integrating automated systems into your snack packaging line offers numerous benefits, from increased efficiency and cost savings to enhanced quality control. Key machines like multihead weighers, vertical form-fill-seal systems, and palletizing robots work together to optimize the entire packaging process, ensuring consistent, high-speed production. By implementing a fully integrated packaging system, snack manufacturers can meet growing demand while maintaining quality and minimizing operational costs.
To stay competitive in the fast-paced snack industry, manufacturers should consider upgrading to an automated system that enhances speed, flexibility, and scalability. The future of snack packaging is automated – are you ready to join the revolution?