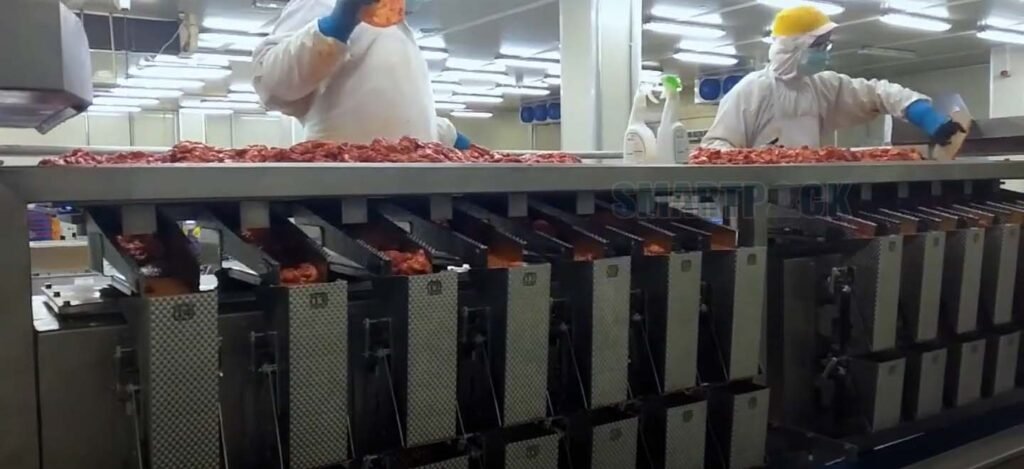
Introduction
If you’re in the meat processing business right now, you’re probably feeling the heat. Honestly, it’s a tough environment out there. You’re dealing with so much at once – finding enough people, keeping costs down, making sure you’re not wasting product, and still delivering top-notch quality. It’s definitely not easy, and the old ways of doing things just aren’t cutting it anymore. We’ve got to adapt and find smarter solutions to stay ahead.
Sound familiar? You’re not alone. Every day, meat processors are facing the same pressures. Are you constantly worried about being short-staffed? Do you cringe when you see how much product ends up as waste? These aren’t just minor annoyances – they’re real problems hitting your bottom line and making it harder to compete.
This blog post is here to help. We’re going to break down the biggest challenges meat packing operations are facing today – the struggle to find labor, the profit drain of product waste, and the constant need to maintain quality and consistency. But more importantly, we’re going to talk about real, practical meat packing solutions. Solutions that can help you not just get by, but actually get ahead and build a more profitable, more resilient business. Because these days, investing in better processes and smarter tech isn’t just a bonus – it’s the key to success.
Let’s Talk Pain Points: What Are the Real Challenges?
Before we jump into solutions, let’s really dig into the problems. Because to fix something, you’ve gotta understand what’s actually broken, right?
Human vs. Automatic Weighing & Packing: A Side-by-Side Comparison for Meat Processors
Feature / Metric | Human/Manual Weighing & Packing | Automatic Weighing & Packing (e.g., Smartpack Systems) | Advantage of Automation |
---|---|---|---|
Accuracy & Precision | Variable: Prone to human error, fatigue, inconsistency. Can lead to over-portioning (“giveaway”). | Consistent & High: Achieves precise weights with minimal deviation. Minimizes giveaway, ensures portion accuracy. | Significantly Improved Accuracy: Reduced product waste, consistent portion sizes, higher yield. |
Speed & Throughput | Lower & Limited: Speed dependent on individual worker pace. Can be bottleneck in high-volume production. | High & Consistent: Processes portions and packages at high, continuous speeds. Dramatically increases throughput. | Increased Speed & Throughput: Handles larger volumes, meets demanding schedules, improves efficiency. |
Labor Requirements | High: Requires a significant number of workers for weighing, packing, and quality control. Vulnerable to labor shortages. | Lower: Automates key processes, reducing the need for manual labor. Frees up staff for other tasks. | Reduced Labor Dependence: Lower labor costs, mitigates impact of labor shortages, optimizes workforce allocation. |
Consistency & Quality | Inconsistent: Quality and presentation can vary due to human factors. More susceptible to errors in sealing, labeling, etc. | Highly Consistent: Delivers uniform portions, packaging, seals, and labeling. Ensures consistent product quality and presentation. | Enhanced Consistency & Quality: Meets higher quality standards, improves brand image, reduces customer complaints. |
Product Waste | Higher: Inherent giveaway in manual weighing. Potential for more product damage due to manual handling and less robust packaging. | Lower: Precision weighing minimizes giveaway. Gentle handling systems and robust packaging reduce product damage and spoilage. | Reduced Product Waste: Lower material costs, higher yield, improved profitability, better sustainability. |
Hygiene & Food Safety | Potentially Lower: Relies heavily on human hygiene practices. More touch points increase contamination risk. | Higher: Automated systems with hygienic designs reduce human contact. Easier to clean and sanitize. | Improved Hygiene & Food Safety: Reduces contamination risks, simplifies sanitation, supports food safety compliance. |
Long-Term Costs | Higher Operational Costs: Higher labor costs, potential for more waste, inconsistencies can lead to rework/returns. May have lower upfront cost. | Lower Operational Costs: Reduced labor, minimized waste, improved efficiency offsets initial investment over time. | Lower Long-Term Operational Costs: Faster ROI through labor savings, waste reduction, and efficiency gains. |
Scalability & Flexibility | Limited Scalability: Increasing output requires adding more manual labor, which can be challenging and costly. | Easily Scalable: Can handle increased production volumes with minimal additional labor. Flexible for different product and packaging types. | Improved Scalability & Flexibility: Adapts to growth and changing market demands, handles diverse product lines. |
The Labor Crunch: Too Much Work, Not Enough People
You’ve seen the headlines, you’re living it every day: finding and keeping good people in meat processing is a real headache. It’s not just your plant; it’s an industry-wide problem. Think about it – the workforce is getting older, the work is demanding, and there are tons of other industries out there competing for workers with what can seem like easier or more appealing jobs. It all adds up to a serious shortage of folks on the line.
So, what does this labor shortage mean for your operation? It’s more than just being short-handed. It creates a domino effect of problems:
- Slower Production Lines
- Overtime Overload
- Quality Can Slip
- Missed Deadlines and Lost Business
If you can’t get orders out on time because of production delays, you risk losing customers and damaging your reputation. It’s a tough spot to be in.
In today’s world, automation isn’t just a “nice to have,” it’s a “must have.” It’s how you keep your production up, stay efficient, and maintain quality, even when you’re short on staff.
Product Waste: A Silent Profit Killer You Can’t Ignore
Okay, let’s talk about something nobody likes to think about too much: waste. In meat packing, it’s a huge issue, and it’s costing you money every single day. From the moment the meat comes in to when it goes out packaged, there are tons of places where product can get wasted. Whether it’s weighing errors, over-portioning, or packaging problems leading to spoilage, product waste is a real drain on your profits.
Where exactly is this waste coming from? Think about:
- Weighing “Giveaway” – Literally Giving Away Product
- Inconsistent Portions = Unhappy Customers
- Spoilage from Bad Packaging
- Damage During Shipping
Weak packaging can also mean damage during transit. Crushed boxes, broken packages – it all leads to unsellable product arriving at its destination.
The dollars and cents of product waste are serious. Those little losses? They snowball. They eat away at your profit margins, mess with your sustainability goals, and tie up money that could be used to grow your business. That’s why getting serious about precision weighing and solid packaging is absolutely critical – it’s how you fight back against product waste and protect your profits.
Quality and Consistency: Meeting Today’s High Expectations
Consumers today? They expect a lot. They want top-quality meat, sure, but they also want it to be consistent every single time. Accurate weights, good presentation – it all matters. Meeting these expectations isn’t optional; it’s how you build your brand, get repeat business, and stand out in a crowded market.
But hitting that quality and consistency mark? That’s tough, especially if you’re relying heavily on manual processes. Here’s why it’s such a challenge:
- Human Error
- Meat Size is Variable
- Regulations are Getting Tougher
If you drop the ball on quality and consistency, there are real consequences. Your brand takes a hit, customers leave bad reviews, you might even face product recalls or fines. On the flip side, automated systems give you the precision and consistency you need to not just meet, but exceed quality standards. That keeps you compliant, keeps customers happy, and builds a rock-solid reputation.
Real Solutions: Tech to the Rescue
Okay, we’ve laid out the problems pretty clearly. But here’s the good news: there are great solutions out there. The answer is in using Smartpack technology to tackle these issues head-on, especially when it comes to weighing and packaging. Let’s take a look at how.
(A) Smartpack Belt Combination Weigher Tray Denesting Machine for Meat
Handling sticky, irregularly shaped fresh or frozen meat portions can be one of the most challenging tasks on a meat processing line. This integrated solution combines the precision and gentle product handling of a Belt Combination Weigher with an automated Tray Denester to seamlessly dispense and load trays. Designed to expertly manage even the most challenging sticky and variable-sized meat portions, from fresh cuts to individual frozen pieces, this system delivers unparalleled efficiency, accuracy, and product presentation for meat processors dealing with demanding product types.
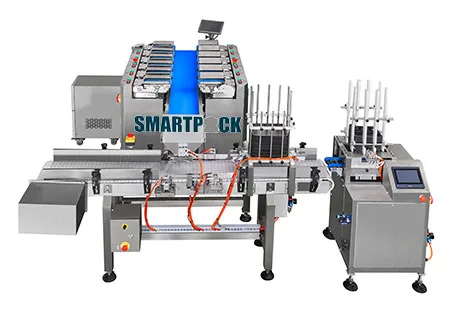
Highlights
- Delicate Handling: Surface protection: Designed with a 30mm drop height to minimize surface imperfections.
- Multi-Functional Convenience: Versatile and space-saving: Combines the function of many devices into one compact unit.
- Effortless Upkeep: Water-washable for easy cleaning: Low maintenance design.
- Compact Footprint: Small and unobtrusive: Compact design for any setting.
(B) Smartpack Meat Multihead Weigher Pouch Packing Machine
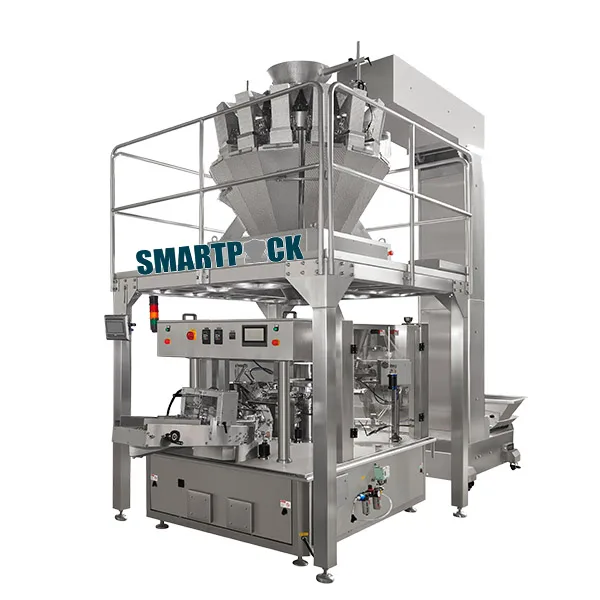
This integrated system pairs the high-speed precision of a Multihead Weigher with a versatile Pouch Packing Machine to deliver a fully automated packaging line. Specifically designed for granular and uniformly shaped meat products like nuggest, meatballs, frozen dumplings and etc., this system ensures rapid, accurate weighing and filling into attractive, consumer-ready pouches – maximizing throughput, minimizing product giveaway, and enhancing shelf appeal for your product range.
The Smart Investment: It’s About More Than Just Machines
Investing in better meat packing tech, like the Smartpack Belt Combination Weigher and Meat Pouch Packing Machine, isn’t just about buying new equipment. It’s about making a smart move for the long-term health and success of your business. It’s about building a more efficient, more profitable, and more reliable operation for the future. Think about the real impact – the Return on Investment (ROI), it’s a win-win investment.
Ready to Make a Change for the Better?
The challenges in meat packing today? They’re definitely real – labor shortages, product waste, keeping up with quality demands. But here’s the thing: within those challenges, there’s a huge opportunity. The opportunity to use smart innovation and technology to build a better, more efficient, and more profitable business.
By bringing in smart tech like the Smartpack Belt Combination Weigher and Meat Packing Machine, you can directly tackle those pain points, unlock real improvements in your operations, and set your business up for long-term success in a changing industry.
So, what’s next? Ready to see how Smartpack can help your operation? Let’s chat about your needs. Contact us today for a quick, free consultation. We can talk about your specific challenges and show you how Smartpack solutions could work for you.
The meat packing industry is changing fast. Smartpack is here to provide you with the innovative tech and expert support you need to not just keep up, but to really lead the way into a more efficient, sustainable, and quality-focused future.