Introduction
Pouch packaging machines are essential for efficient production in industries ranging from food and beverage to pharmaceuticals. The design of these machines plays a critical role in determining their application, speed, and efficiency. Here, we’ll explore pouch packaging machines from their designs and mechinical structure to understand the types of machine. So, what are the common types pouch packaging machine?
Horizontal Form Fill Seal (HFFS) Machines
Horizontal Form Fill Seal (HFFS) machines are designed to handle packaging processes horizontally. The machine forms pouches from a roll of film, fills the product, and then seals the pouch, making it a versatile solution for a wide range of products.
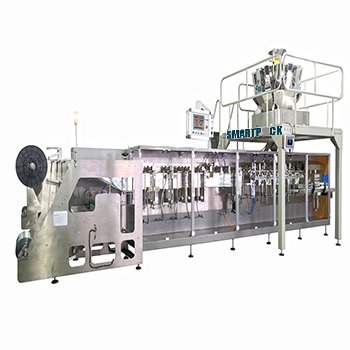
How It Works:
- The film is fed horizontally into the machine.
- The machine forms pouches, fills them with the product, and seals the pouch.
- Ideal for products that need to remain upright or require additional features such as zippers.
Best Suited For: Premade flat pouches or stand up pouches directly from film.
Applications: Snack foods, confectionery, pharmaceuticals, comestics and household products.
Advantages:
- High-speed production and versatile pouch designs.
- Minimal film waste due to precise cutting.
- Suitable for a variety of pouch shapes and sizes.
Rotary Pouch Packaging Machines
Rotary pouch packaging machines work in a circular motion and are equipped with multiple stations that fill, seal, and print pouches as they rotate. These machines are well-suited for pre-made pouches and provide an efficient method for packaging liquids, powders, and granules.
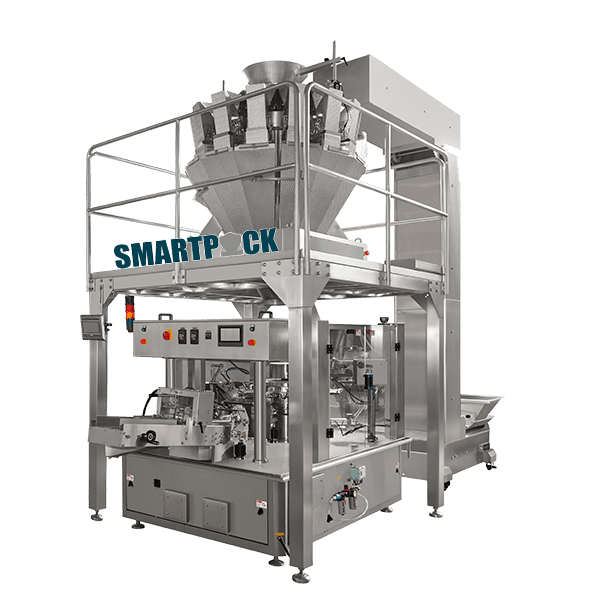
How It Works:
- Premade pouches are loaded into the machine, where they move through various stations (filling, sealing, coding, and labeling) in a rotary fashion.
- The circular motion ensures high efficiency and quick changeover between pouch sizes.
Best Suited For: Premade pouch filling and sealing operations.
Applications: Used in industries handling liquids, powders, and granular products like sauces, coffee, and pet food.
Advantages:
- High flexibility for handling different pouch sizes.
- Efficient for medium to high production volumes.
- Faster changeover times, reducing downtime.
Vacuum Pouch Packaging Machines
Vacuum packaging machines play a crucial role in prolonging product shelf life by removing air from the pouch and creating an airtight seal. This process protects products from oxygen, moisture, and contaminants, making vacuum packaging ideal for products requiring preservation.
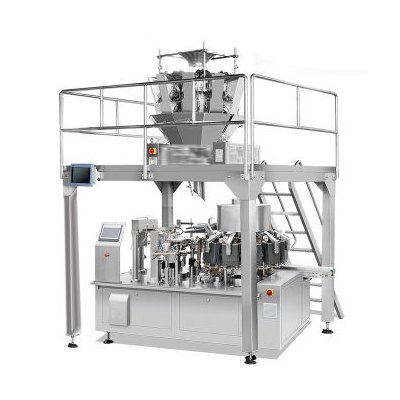
How It Works:
- The machine first fills the pouch with the product.
- The pouch is then vacuum-sealed, removing most or all of the air before sealing it shut.
- Optional gas flushing may be applied for products needing specific atmospheric conditions inside the package.
Best Suited For: Products that are sensitive to oxygen exposure and need extended shelf life.
Applications: Vacuum pouches are commonly used for packaging meat, seafood, dairy products, coffee, pharmaceuticals, electronics, and even fresh produce.
Advantages:
- Extends the shelf life of perishable products.
- Protects products from moisture, oxygen, and external contaminants.
- Often used in conjunction with gas flushing to create modified atmosphere packaging (MAP).
- Reduces packaging volume, making storage and transportation more efficient.
Machine Designs:
- Chamber Vacuum Packaging Machines: These machines are ideal for batch production, where pouches are placed in a vacuum chamber, air is removed, and then the pouch is sealed.
- External Vacuum Sealers: These machines are designed for large-scale operations, where the product remains outside the vacuum chamber, and the machine only seals the pouch by removing air.
Additional Benefits:
- Reduces the need for chemical preservatives.
- Ensures food safety and quality for longer durations.
- Maintains the integrity and freshness of delicate electronic components.
Industries: Food and beverage, medical, electronics, and any industry that requires a sterile or air-tight packaging environment.
Fully Automated vs. Semi-Automated Pouch Packaging Machines
The level of automation plays a key role in choosing a pouch packaging machine, with options ranging from fully automated systems to semi-automated machines.
Fully Automated Machines: These machines manage the entire process from pouch formation to sealing without requiring manual intervention. They are ideal for high-volume production environments.
Best Suited For: Large-scale operations where speed and consistency are paramount.
Advantages:
- Increased production efficiency.
- Minimal labor costs.
- Consistent and reliable output.
Semi-Automated Machines: These machines require manual input at various stages, making them more suitable for smaller businesses or operations with more flexible packaging requirements.
Best Suited For: Smaller or niche operations with frequent changeovers or customization needs.
Advantages:
- Cost-effective for small and medium businesses.
- Greater control over smaller production runs.
Conclusion
Choosing the right pouch packaging machine involves understanding the differences in machine design and their intended applications. From the high-efficiency vacuum pouch packaging machines to flexible rotary and multi-lane systems, manufacturers must consider their production volume, product type, and budget when selecting the ideal machine. The future of pouch packaging will continue to trend toward increased automation and more flexible, customized solutions.