
Volumetric cup filler machines simplify packaging processes by delivering precise, consistent product volumes into containers. These efficient filling machines are critical in industries such as food processing and chemicals, where product uniformity is non-negotiable.
What is the Working Principle of Volumetric Cup Filler Machine?

The precision of volumetric cup fillers lies in their straightforward yet effective design. Adjustable, calibrated cups measure specific product volumes. As the product fills the cups, the machine dispenses exact quantities into containers, ensuring uniformity every time.
Measure Cup Filler Machine Key Features
- User-Friendly Design: Intuitive controls allow operators to easily manage the machine with minimal training.
- Maintenance-Friendly Construction: Modular designs simplify disassembly for cleaning and maintenance, minimizing downtime.
- Speed and Precision: Optimized for high-volume production, these machines deliver accurate fills at impressive speeds.
- Durable Materials: Built with robust, non-corrosive materials like stainless steel, they are engineered for demanding industrial environments.
- Durable Plastic: Constructed with high-quality, durable plastic, ensuring longevity and reliability in various conditions.
- Fine Tune: The ability to fine tune the machine allows for precise fills, accommodating specific product specifications.
Applications
Versatile and dependable, volumetric cup fillers handle powders, granules, and other free-flowing materials. They meet diverse industry needs and are used across industries:
- Chemicals for granular substances.
- Food Products like rice, sugar, beans and spices.
A volumetric cup filler typically integrates seamlessly with vertical packing machines to create a highly efficient and automated packaging system. The volumetric cup filler accurately measures and dispenses a specific volume of product, while the vertical packing machine forms, fills, and seals the packaging material. This combination ensures a streamlined process where products are consistently measured and securely packaged, ideal for industries requiring precision and speed. Together, they handle a wide range of materials, from powders to granules, enhancing productivity and maintaining product quality across various production lines.

Advantages
- Cost-Effective: Provides an affordable packaging solution without sacrificing performance.
- Uniform Fills: Reliably measures by volume for consistent quantities.
- Adaptable: Adjustable cup sizes accommodate a range of product types and volumes.
- Waste Reduction: Precision filling minimizes product loss.
Limitations
- Density Variations: Measuring by volume rather than weight can result in discrepancies for products with variable densities.
- Material Flow Challenges: Sticky or non-free-flowing products may impact performance and consistency.
Comparison with Other Fillers
- Auger Fillers: Superior for fine powders but typically more complex and costly.
- Multi-Head Weighers: Offers unparalleled weight accuracy but requires a higher initial investment.
- Liquid Pump Fillers: Tailored for liquid products, a stark contrast to volumetric cup fillers.

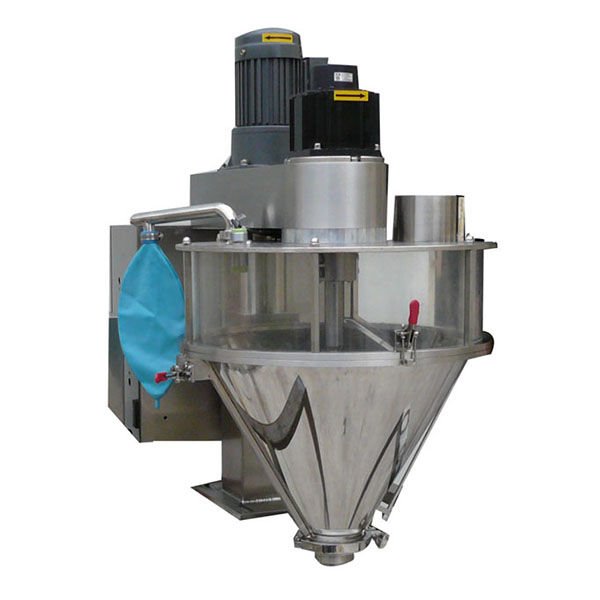
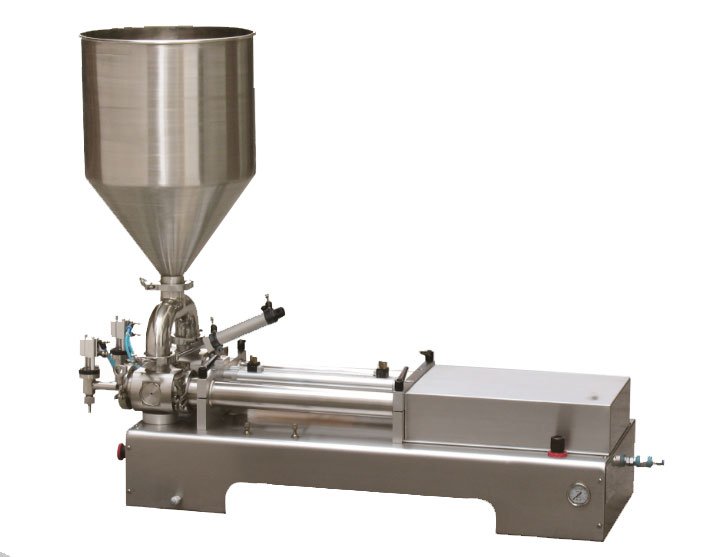
Maintenance and Safety
- Routine Cleaning: Ensures hygiene and product quality.
- Calibration Checks: Regularly validate cup settings for accurate fills.
- Operator Safety: Incorporate safety features like guards and emergency stops.
- Cleaning Process: The design simplifies the cleaning process, making it more convenient and ensuring the machine remains in optimal condition.
Conclusion
Volumetric cup fillers strike a balance between affordability, efficiency, and versatility. They deliver reliable performance across industries, though considerations like product characteristics and accuracy requirements should guide their selection. When precision and simplicity matter, these machines stand out as a trusted solution in modern packaging lines.