Frozen food manufacturers are constantly facing the challenge of balancing rising costs with the need for faster production and consistent quality. Robotic automation has emerged as a key solution to these challenges, as highlighted by the success of one major frozen food producer. By implementing robotics in their packaging operations, they were able to slash labor costs while significantly increasing speed and throughput. This case study delves into how the company transformed its packaging process, driving efficiency and maintaining high standards, setting a new industry standard for operational excellence.
Case Study
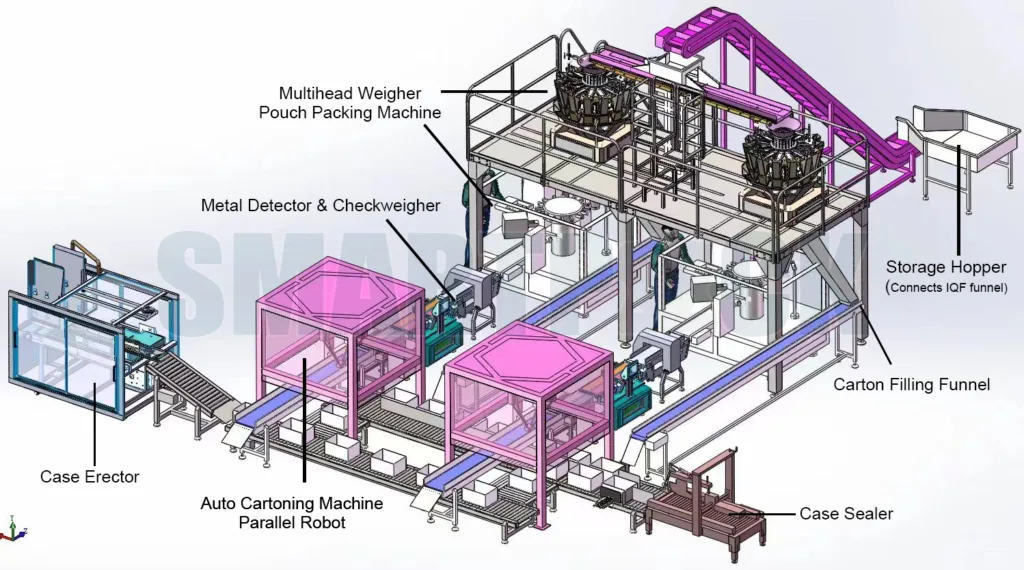
Performance Details
The automated shrimp packaging line showed impressive speed and efficiency, achieving the following performance results:
- 400 Grams Pouch: 45 packages per minute/unit, 90 packs/min for whole system; Pouch size: 270 x 180 mm
- 1000 Grams Pouch: 30 packages per minute/unit; Pouch size: 320 x 220 mm
- 2000 Grams Pouch: 20 packages per minute/unit; Pouch size: 390 x 270 mm
Speed Performance:
- Rotary Pouch Packaging Machine: Capable of processing 40 pouches per minute, ensuring consistent quality and accuracy in every package.
- Carton Packing Machine: Handles up to 25 cartons per minute, seamlessly integrating into the overall packaging line to maintain a steady flow of prepared cartons.
In addition to the pouch packaging, Smartpack designed additional tunnels for filling cartons with heavier weight to meet customer’s requirement.
Background of Smartpack
Smartpack is a leading innovator in the field of packaging automation, specializing in delivering robotic solutions tailored to the food industry. One of their standout projects involved a collaboration with a frozen shrimp producer, who faced several key challenges in their packaging operations. Despite strong demand, the company struggled with escalating labor costs, slow production speeds, and inconsistent packaging quality—issues that affected both their profitability and their ability to meet market needs.
The Implementation of Robotics
To overcome these hurdles, Smartpack designed and implemented a fully automated shrimp packaging line, utilizing robotic arms, automated sorting systems, and state-of-the-art vision technologies. The solution was tailored specifically to meet the unique needs of shrimp packaging, where products must be handled delicately, remain frozen, and be packaged with high speed and precision.
- Initial Research and Selection: Smartpack worked closely with the client to understand their operational pain points and develop a customized automation plan. After thorough research and system evaluations, they selected robotics systems that would improve both speed and consistency in packaging.
- Installation and Trial Phase: The installation of the robotic line took place over several weeks, including a comprehensive trial period to fine-tune system operations and ensure seamless integration with the client’s existing production infrastructure.
Technologies Adopted
The automation solution integrated into the shrimp packaging line included several key technologies designed to enhance efficiency and reduce reliance on manual labor:
- Robotic Arms: These robots were used for the precise handling of shrimp, placing the delicate products into trays or boxes with minimal handling, ensuring both speed and safety.
- Collaborative Robots (Cobots): Cobots were introduced to work alongside human operators, assisting in quality checks and packaging. This allowed for faster adjustments and quality control, improving the overall efficiency of the line.
- Vision Systems: High-tech vision systems were implemented to ensure the shrimp were correctly placed and packaged. The vision technology also performed quality checks to ensure packaging integrity, catching defects before they reached customers.
The frozen food industry faces several challenges in an increasingly competitive market. Rising labor costs, slow production speeds, and the growing need for consistent, high-quality packaging are just a few of the hurdles that manufacturers must overcome. As demand for frozen foods rises globally, companies are under pressure to maintain production efficiency while meeting stringent quality standards.
One promising solution to these challenges is robotic automation. By integrating robots into the packaging process, manufacturers can reduce labor costs, increase speed, and enhance packaging consistency. In this blog, we will explore a case study of a frozen food company that successfully adopted robotic automation in their packaging line, showcasing the benefits and challenges along the way.
The Need for Automation in Frozen Food Packaging
Overview of the Frozen Food Industry
Frozen food demand has been on the rise, with consumers seeking quick and convenient meal options. This growth trend has created significant pressure on manufacturers to scale production while ensuring that products remain fresh, high-quality, and safely packaged. However, traditional packaging methods—often reliant on manual labor—pose several challenges:
- High Labor Costs: Labor wages continue to climb, creating a financial strain for many frozen food manufacturers.
- Speed Constraints: Manual packaging is often slower than automated systems, hindering the ability to meet growing demand.
- Consistency Issues: Achieving uniformity in packaging, especially with perishable frozen products, is a significant concern.
Labor Costs in the Frozen Food Industry
Labor shortages and rising wages have placed a heavy burden on manufacturers, particularly those in labor-intensive industries like frozen food packaging. As the demand for frozen products increases, businesses are forced to hire more workers, which compounds the financial strain. Additionally, manual processes are prone to inconsistencies and errors—leading to packaging mistakes, product damage, and inefficiencies.
Speed and Efficiency Demands
Today’s consumers expect faster production and delivery times. Frozen food manufacturers must increase throughput without compromising on product quality or safety. As companies scale production, the need for speed and efficiency in packaging becomes even more critical. This is where robotic automation can make a significant difference.
Introduction to Robotic Automation in Food Packaging
What is Robotic Automation?
Robotic automation involves the use of robots to perform tasks traditionally done by human workers. In food packaging, automation typically includes the use of:
- Robotic Arms: These are often used for picking, placing, and packing food items into boxes or trays.
- Collaborative Robots (Cobots): Cobots work alongside human operators to handle tasks such as packaging and quality control in a safer, more efficient manner.
- Automated Guided Vehicles (AGVs): These robots transport products through the production line with minimal human intervention, improving overall efficiency.
Why Robotics for Frozen Food?
Robotic automation is particularly well-suited for the frozen food industry for several reasons:
- Cold Environments: Many robots are designed to function in cold environments, making them ideal for frozen food packaging lines where temperatures often dip below freezing.
- Harsh Conditions: Robotics can operate in environments that may be too harsh or unsafe for human workers, such as handling frozen food at high speeds.
- Improved Safety: Robots can take over repetitive and hazardous tasks, reducing the risk of workplace injuries.
The Results of Robotic Automation
Reduction in Labor Costs
The integration of robotic automation in the shrimp packaging line led to significant savings in labor costs. By replacing manual labor with robotics, the shrimp producer reduced the number of workers required for packaging tasks. The automated system handled repetitive and time-consuming tasks, allowing human workers to focus on more specialized roles. This not only reduced labor expenses but also minimized the risk of errors and inefficiencies associated with manual handling.
Increased Speed and Throughput
Robotic automation significantly boosted production speed and throughput.
With the rotary pouch packaging machine processing up to 45 pouches per minute, the overall throughput was dramatically increased compared to previous manual processes. This speed allowed the company to meet growing demand and ensure quick turnaround times, all while maintaining consistent quality and minimizing the risk of delays.
Consistency and Quality Control
The introduction of vision systems and robotic arms greatly improved packaging consistency. The vision technology ensured that every pouch was accurately filled and sealed, preventing packaging defects and ensuring product integrity. This automated approach minimized human error and enhanced the overall quality control process, making sure that each package met the highest standards.
The automated sorting system further contributed to consistency by sorting shrimp based on size and weight, ensuring each package met exact specifications. This reduced variations between packages, leading to more uniform and reliable products.
Employee Impact and Workplace Safety
The shift to robotic automation not only improved operational efficiency but also enhanced workplace safety. Robots took over the repetitive, physically demanding tasks, reducing the risk of worker fatigue and injury. Human employees were able to transition to more supervisory and maintenance roles, which helped boost morale and job satisfaction. With the automation system in place, the workplace became safer, more efficient, and more rewarding for employees.
The end result was a dramatic improvement in both speed and quality, with the shrimp packaging line becoming more efficient, consistent, and safer than ever before.
Key Challenges
Challenges During Implementation: The Harsh Environment
One of the key challenges Smartpack faced during the implementation of robotic automation in the shrimp packaging line was the harsh working environment. The frozen food industry, especially shrimp processing, often requires operations to be conducted in low-temperature and high-humidity conditions. These conditions are difficult for many automation systems, as they can lead to performance issues, wear, and potential breakdowns of the equipment.
However, Smartpack overcame this obstacle by customizing the robotic machines to be specifically designed to function in such environments. The systems were engineered with materials and components capable of withstanding cold temperatures and high moisture levels. This ensured that the robotic arms, vision systems, and sorting equipment could perform reliably and consistently, even in sub-zero temperatures and humid conditions commonly found in frozen food packaging lines.
Advice for Other Frozen Food Manufacturers
For other frozen food manufacturers looking to implement robotic automation, Smartpack advises investing in machines designed specifically for low-temperature and high-humidity environments. Customization and careful selection of materials can prevent operational failures and extend the lifespan of the automation system. Furthermore, working closely with automation experts who understand the intricacies of the frozen food industry can help companies overcome these environmental challenges and ensure smooth, continuous production.
The Future of Robotic Automation in Frozen Food Packaging
The field of robotic automation continues to evolve. Future innovations, such as Delta robots for auto cartoning and more advanced collaborative robots for palletizing, will further optimize food packaging systems. These robots will be able to learn from their environment, improving efficiency and reducing downtime. Manufacturers will also see increased adoption of machine learning algorithms that predict potential problems in the production line before they occur.
As robotic solutions become more affordable and scalable, manufacturers will have more opportunities to expand their automation systems. This could include scaling systems for larger production runs or multi-site operations. Robotic automation will also become increasingly adaptable, allowing manufacturers to switch between different product lines with minimal reconfiguration.
Conclusion
Robotic automation has proven to be a transformative solution for frozen food manufacturers, addressing the key challenges of rising labor costs, slow production speeds, and the need for consistent packaging quality. As demonstrated in the case study of Smartpack’s customized shrimp packaging line, automation not only reduces labor costs but also significantly increases production speed, ensures greater consistency, and improves overall product quality.
By adapting robotic systems to work efficiently in low-temperature and high-humidity environments, Smartpack’s client was able to streamline operations and meet the growing demand for frozen shrimp while maintaining high standards. The result was a more efficient, cost-effective, and safer packaging process.
For frozen food manufacturers looking to stay competitive, robotic automation is no longer just an option-it’s a necessity. By investing in automation, companies can not only enhance their production capabilities but also improve product quality, reduce costs, and create safer, more productive workplaces.
Explore Robotic Solutions for Your Packaging Line
If you’re considering integrating robotic automation into your packaging line, Smartpack can help you take the first step. Reach out to our experts at info@smartpackmc.com for personalized consultation and guidance on how our customized solutions can transform your packaging operations and boost your efficiency.