Use our comprehensive guide to jar packing machines to revolutionize your packaging operation. Learn about the kinds, characteristics, and upcoming trends that can precisely and efficiently transform your processes.
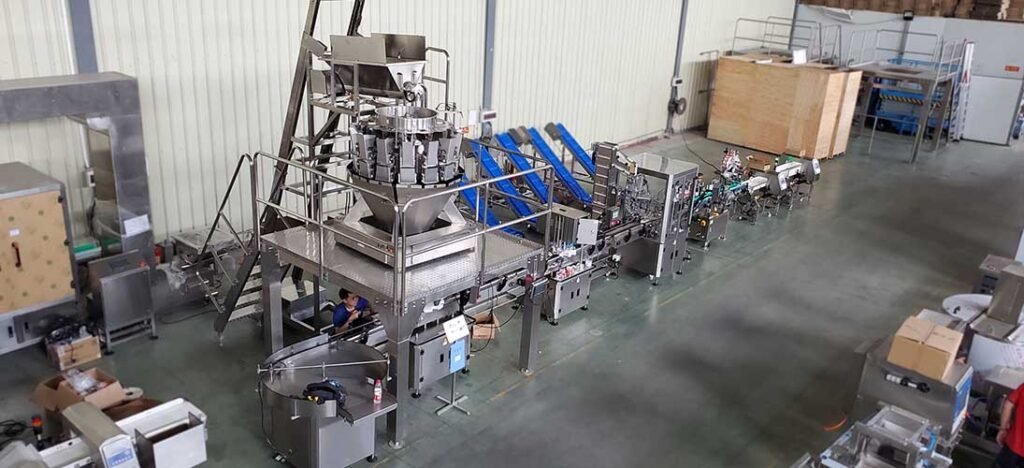
Introduction
In today’s competitive manufacturing environment, efficiency and innovation are key drivers of success. Businesses in industries like food, cosmetics, and pharmaceuticals are increasingly turning to automated solutions to optimize their production lines. Among these innovations, jar packing machines have emerged as essential tools for streamlining operations and maintaining consistent quality.
This comprehensive guide explores everything you need to know about jar packing machines—from their types and key features to the benefits they bring and the latest technological trends shaping the industry. Whether you’re looking to boost productivity, enhance product presentation, or scale your operations, this guide will help you make an informed choice for your business.
Increasing operational efficiency is critical to corporate success in the fast-paced manufacturing and packaging industries of today. Choosing a jar packing machine can be crucial to revolutionizing your production line, regardless of whether you work in the food, cosmetics, or pharmaceutical sectors. The complexities of jar packing machines, their advantages, and how to select the best option for your company are all covered in this article.
What Is a Jar Packing Machine?
A jar packing machine is specialized equipment designed to automate the weighing, filling, sealing, capping, and labeling of jars containing various products. This includes the use of a filling machine, which is a type of jar packing machine that handles the precise filling of granule, powder, liquids, sauces, and pastes into jars. These machines cater to a wide range of industries, including food (e.g., nuts, jams, sauces, and spices), cosmetics (e.g., creams and lotions), and pharmaceuticals (e.g., supplements and ointments).
Key components of a typical jar packing machine line include:
Weighing Machine
Ensures accurate measurement of the product before filling, maintaining consistency in the jar’s content and complying with industry standards. It uses load cells and precision sensors to achieve the required product weight per container.
Filling Machines
Ensures precise filling of liquid, semi-liquid, or granular products. Advanced models can be adjusted for viscosity, density, and flow rates, preventing overflows and product wastage.
Foil Sealing Machine
Applies an airtight foil or membrane to the jar’s opening after filling, preserving freshness, preventing contamination, and extending product shelf life. The foil may be heat-sealed or induction-sealed for a secure, tamper-evident closure.
Capping Machine
Secures jars with caps or lids, ensuring a tight seal. This step helps maintain product integrity and prevents spillage. Many systems are adjustable to accommodate various cap sizes and styles.
Labeling Machine
Applies accurate and visually appealing labels, conveying essential product information and enhancing brand identity. The labeling process often includes options for front, back, wrap-around, or tamper-evident labels.
Conveyor System
Automates the transportation of jars through various stages of the production line. A well-designed conveyor system streamlines workflow, reduces manual handling, and improves overall efficiency.
By automating these processes, jar packing machines enhance efficiency, reduce labor costs, and maintain consistent product quality. This integrated approach allows businesses to meet regulatory requirements, satisfy consumer expectations, and sustain competitive advantage in the marketplace.
Types of Jar Packing Machines
Jar packing machines come in various configurations to suit different production scales and product types. Below are the most common types:
Automatic Jar Packing Machines
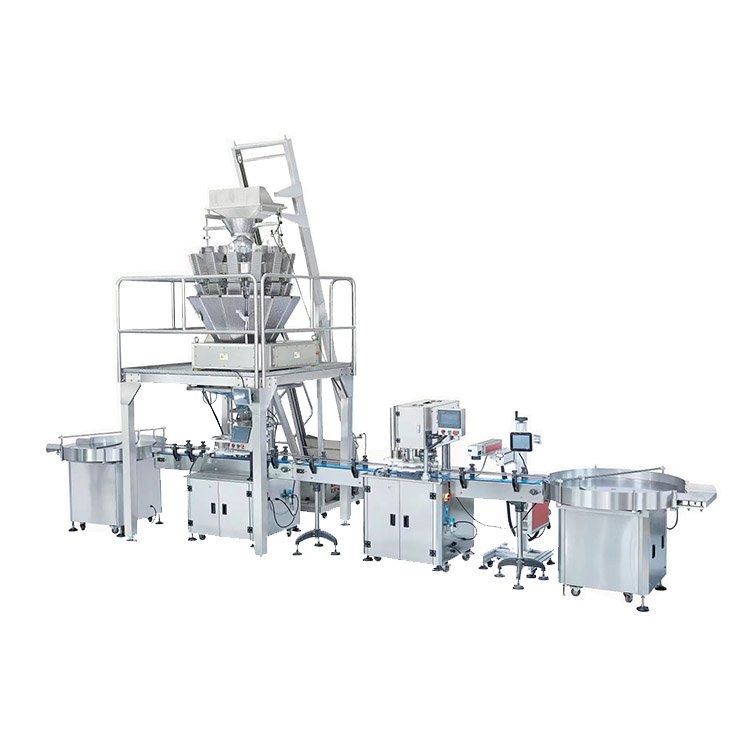
- Features: Fully automated operations, capable of handling high production volumes with minimal human intervention.
- Applications: Ideal for large-scale manufacturers needing speed and precision.
- Benefits:
- High-speed production.
- Consistent and accurate packaging.
- Reduced labor costs.
Semi-Automatic Jar Packing Machines
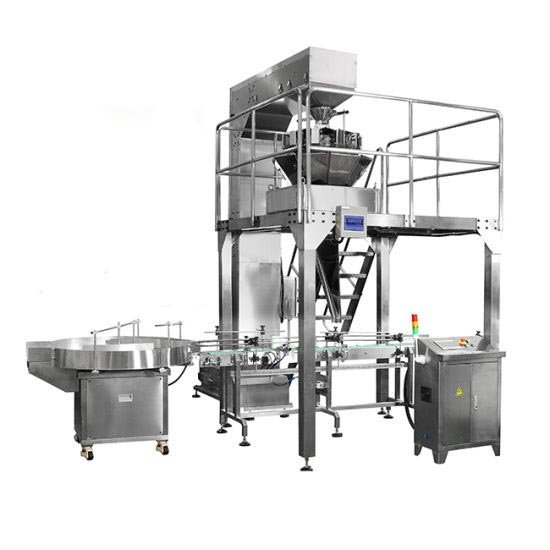
- Features: Require some manual input but automate key processes like filling and capping. The filling volume in semi-automatic machines can be easily adjusted, ensuring precise dosing for various container sizes and types.
- Applications: Suitable for small to medium enterprises.
- Benefits:
- Cost-effective solution for businesses with moderate production needs.
- Greater control over specific stages of the process.
Customized Jar Packing Machines
- Features: Tailored designs to meet unique operational requirements, such as handling non-standard jar sizes or integrating with existing systems.
- Applications: Businesses with specific packaging needs, such as handling fragile glass jars or specialized sealing techniques.
- Benefits:
- Enhanced flexibility.
- Ability to accommodate diverse product ranges.
How Do Jar Filling and Packing Machines Work?
Understanding the operational flow of jar packing machines helps businesses optimize their use. Here’s a step-by-step breakdown:
Feeding: Empty jars are placed on the conveyor system, either manually or automatically. The conveyor then transports these jars into the production line at a controlled speed.
Weighing: Before the filling process, the jars (or the product) are weighed to ensure that each container receives the correct amount of product. Weighing stations use high-precision load cells or other sensors to detect and control the weight, enabling uniform product distribution, compliance with industry standards, and minimal product wastage.
Filling: A precise filling system dispenses the product into the jars. This system varies depending on the product’s nature:
- Gravity Fillers for Thin Liquids: Utilize the natural force of gravity to feed liquid into containers through nozzles.
- Piston Fillers for Thick Pastes: Employ a retractable piston mechanism to draw product into a cylinder and then push it out into the jar, ensuring accurate volumetric filling.
- Auger Fillers for Powders: Use a rotating auger screw to consistently dispense powdered products into jars.
- Multihead Weighers for Granules: Multiple weighing heads feed product into a central chute, optimizing accuracy by selecting the best combination of partial weights to achieve the target fill weight.
Foil Sealing: Induction sealing machines apply electromagnetic induction to heat an aluminum foil liner, bonding it securely to the jar’s rim. This creates a hermetic seal that maintains freshness, prevents leakage, and provides a tamper-evident barrier.
Capping: After sealing, capping machines place and tighten caps or lids onto the jars. Adjustments can be made to handle various cap sizes, shapes, and materials. A consistent torque ensures a reliable, leak-proof closure that preserves product quality during transportation and storage.
Labeling: Labels are accurately applied to each jar. Modern labeling systems can be configured for different label orientations—front, back, wrap-around, or tamper-evident—and may use sensors or vision systems to ensure proper alignment. Labels enhance brand presentation, provide essential product information, and meet regulatory requirements.
Final Inspection: Quality checks are performed to confirm that each jar meets established packaging standards. This may involve checking fill levels, cap security, label placement, and seal integrity. Automated vision inspection systems or manual spot checks ensure that defective products are identified and removed before shipping.
Secondary Packaging: Once verified, the jars are grouped and placed into secondary packaging, such as cartons or crates, ready for distribution. Automated case packers and palletizers can be employed to streamline this stage, reducing manual labor and improving overall efficiency.
By following these steps, jar filling and packing machines ensure a consistent, high-quality, and efficient production process that benefits both manufacturers and consumers.
Key Features to Look for in a Jar Packing Machine
Selecting the right machine involves evaluating its features against your production needs. Key considerations include:
- Speed and Capacity: Match the machine’s output rate with your production demands.
- Product Compatibility: Ensure the machine handles your product’s viscosity, density, and other properties.
- Jar Size Flexibility: Opt for machines that accommodate a range of jar sizes and materials.
- Automation Level: Determine if a semi-automatic or fully automatic machine aligns with your goals.
- Compliance: Verify that the machine adheres to industry standards like FDA and CE certifications.
- Servo Motor: Look for machines equipped with servo motors to enhance precision and efficiency in the filling process, providing high accuracy in dosing and customizable features for different production needs.
Benefits of Using a Jar Packing Machine in the Food Industry
Investing in a jar packing machine offers numerous advantages, including:
- Enhanced Efficiency: Automated processes significantly reduce production time. The packaging line functions efficiently with minimal manual intervention, ensuring smooth operation.
- Consistent Quality: Precision systems ensure uniform filling, sealing, and labeling.
- Labor Cost Reduction: Fewer operators are needed, lowering operational expenses.
- Improved Hygiene: Machines reduce manual handling, maintaining product cleanliness.
- Scalability: Machines can be upgraded to meet growing production demands. Jar packing machines can adapt to specific market demand, enhancing operational output.
Choosing the Right Jar Packing Machine for Your Business
Here’s a guide to help you select the ideal jar packing machine:
Assess Your Needs
- Identify your production volume.
- Determine the types of products and jars you’ll be packaging, including specific products like edible oil.
Set a Budget
- Consider initial costs and long-term savings from reduced labor and improved efficiency.
Evaluate Features and Production Capacity
- Look for machines with adjustable settings to handle diverse product types.
- Check for additional features like tamper-evident sealing or vacuum sealing.
- Consider the importance of a star wheel for adapting to different jar sizes, ensuring the machine can accommodate various jars for accurate filling processes.
Cost Considerations
The cost of a jar packing machine depends on several factors, including:
- Machine type (semi-automatic vs. automatic). A packaging machine is versatile in handling different jar filling processes, accommodating various automation levels.
- Production capacity.
- Additional features and customizations.
After-Sales Support
- Choose suppliers that offer training, maintenance, and readily available spare parts.
While the initial investment might seem high, the long-term benefits of increased efficiency and reduced labor costs often outweigh the upfront expenses. Additionally, a piston filling machine is cost-effective for various products, offering precise volumetric filling for both thick substances and those with particulates.
Maintenance Tips for Optimal Performance
Proper maintenance ensures your jar packing machine operates efficiently. Key practices include:
- Regular Cleaning: Prevent product buildup that can cause clogs or contamination. Regular cleaning is crucial for maintaining packaging machines to ensure they function efficiently and maintain product quality.
- Lubrication: Keep moving parts well-lubricated to avoid wear and tear.
- Scheduled Inspections: Identify and address potential issues before they escalate.
- Operator Training: Ensure staff are knowledgeable about machine operation and troubleshooting.
Future Trends in Jar Packing Technology
Stay ahead by exploring emerging trends:
- Automation and Robotics: Advanced systems reduce human involvement and improve precision.
- Sustainability: Eco-friendly packaging solutions and reduced energy consumption.
Advanced systems are increasingly used for packaging salad dressings and other food products, ensuring effective sealing and extended shelf life.
Frequently Asked Questions (FAQs)
1. What is the average cost of a jar packing machine?
Prices range from $5,000 for basic models to over $50,000 for single unit machine, or high-end, fully automated systems.
2. Can jar packing machines handle multiple jar sizes?
Yes, many machines offer adjustable settings to accommodate various jar sizes and materials.
3. How long does it take to recover the investment in a jar packing machine?
Depending on production volume, most businesses see ROI within 1-2 years.
Contact
Ready to enhance your packaging efficiency? Contact the SmartPack team today to explore our range of jar packing machines tailored to meet your business needs. Our experts are here to provide personalized consultations, answer your questions, and guide you toward the perfect solution. Request a free demo or detailed product brochure now!
Partner with SmartPack to revolutionize your production line and achieve unparalleled efficiency. Don’t wait—reach out to us and take the first step toward optimizing your operations today!